HESSLITE BONDING MORTAR
VBM PolyThin Bonding Mortars are designed for THINBED bonding applications with mortar beds less than 1/2". Thinbed bonding mortars are intended for use over smooth, even substrates, such as cement backer board, finished concrete, flush-joint masonry units, and gypsum board. Three product variations (performance levels) are available in the VBM PolyThin product class.
VBM PolyThin 100 is a polymer modified, lightweight, THINBED bonding mortar for traditional grouted applications over smooth, even substrates. Combines high bond strength, excellent non-sag and water resistance/efflorescence control properties not found in most mortars. Includes anti-microbial additives. VBM PolyThin 100 is a great combination of high performance and economy for most grouted applications.
SPECIFICATIONS: Level 1 performance product. Meets the property specifications of ANSI 118.4 shear bond (tile). Manufactured in accordance with ASTM C1714.
USES: VBM PolyThin 100 is designed for bonding manufactured stone, natural stone veneers, thin brick, precast concrete, ceramic tiles, certain glass tiles, and similar veneers or pavers (pedestrian traffic) requiring a thin mortar bed (LESS than 1/2"). For interior or exterior applications.
DATA SHEET: VBM PolyThin 100 Lightweight Bonding Mortar • (PDF)
VBM PolyThin 300 is a polymer modified, light-weight, THINBED bonding mortar. Provides enhanced bonding, non-sag, and water repellency performance.
SPECIFICATIONS: Level 2 performance product. Meets the property specifications of ANSI 118.4 shear bond (tile). Manufactured in accordance with ASTM C1714.
USES: VBM PolyThin 300 is designed for THINBED bonding (LESS than 1/2") over smooth substrates. Applications include drystack-type masonry units with limited or no grout joint, cast board forms, pavers (pedestrial traffic), large format tile, and panelized units of manufactured stone or brick. For interior or exterior applications.
DATA SHEET: VBM PolyThin 300 Lightweight Bonding Mortar • (PDF)
SPECIFICATIONS: Level 3 performance product. Meets the property specifications of ANSI 118.15 shear bond (tile). Manufactured in accordance with ASTM C1714.
USES: For THINBED bonding (LESS than 1/2") over smooth substrates. Advanced bonding applications include drystack installations that have limited or no grout joint, stone, brick, and thicker natural stone veneers, large-format profiles, heavy veneers, and high traffic areas. For interior or exterior applications.
DATA SHEET: VBM PolyThin Premium Lightweight Bonding Mortar • (PDF)
Description
Advantages. VBM PolyThin bonding mortars have these advantages:
• Lightweight for easy handling and reduced structural loading (reducing weights by ‹100 lbs/cu.ft.);
• Water repellent/freeze-thaw durability;
• Extra tack and non-sag properties;
• High shear bond strength;
• Low shrinkage.
Colors. Available in standard gray and soft white.
Packaging. VBM PolyThin mortars are available in 35 lb. moisture-resistant bags.
Coverage. Coverage can vary based on job conditions and application thickness. Yield is approximately 0.39 cu.ft. per 35 lb. bag.
1/4" x 1/4" x 1/4" | (6x6x6mm) | 70-80 sq.ft. |
1/4" x 3/8" x 1/4" | (6x9.5x6mm) | 50-60 sq.ft. |
1/2" x 1/2" x 1/2" | (13x13x13mm) | 25-35 sq.ft. |
Shelf Life. When stored in a cool, dry, low humidity area: approximately six months to one year.
Efflorescence. All VBM PolyThin mortars reduce the potential for efflorescence and provide some water repellency, however due to variables beyond our control, we cannot guarantee against efflorescence.
Suitable Substrates. See INSTALLATION; Substrates.
Limitations. Please note and abide by the following limitations:
• Do not apply when temperatures are below 40° F prior to cure;
• Do not add any admixtures without prior consent;
• Follow ANSI, TCA, or ASTM guidelines for installation in high heat, cold or wind;
• Always perform quality control testing before and during application;
• Not recommended over particle board, plywood, Luan, or hard wood floors;
• Not recommended for green marble or water-sensitive stone;
• Do not apply over 1/2-inch thickness.
Technical Data
VBM PolyThin bonding mortars contain Portland Cement (ASTM C150), graded lightweight aggregate, Type-S Lime (ASTM C207), R-Mortar Aid, and proprietary polymer additives. Manufactured in accordance with ASTM C1714. VBM PolyThin bonding mortars meet the shear bond requirements of ANSI - 118.4 Modified Portland Cement Mortar (Tile). VBM PolyThin Premium meets the shear bond requirements of ANSI 118.15.
Open time @ 70°F (23°C) | 20 min |
Adjustability @ 70°F (23°C) | 10 min |
Pot life @ 70°F (23°C) | 2 hrs |
Compressive strength (ASTM C-109) | >2500 psi |
Shear Bond ANSI 118.4 Requirements | ||
Glazed Wall Tile | ||
7 Days | >300 psi | |
Water Immersion | >200 psi |
Installation
Substrates. All substrates must be clean and free from any dirt, oil, paint, bond breakers or any substances which may hinder bond. The substrate must be structurally sound and conform to good engineering practices. Substrate deflection under all live, dead and impact loads, including concentrated loads must not exceed L/360 for thin bed installation or L/480 for thick bed stone installations, where L= span length. Installations shall be in accordance with applicable building codes. Movement joints shall be brought through mortar and veneer to the surface. Suitable substrates include:
• Lath and Cement Plaster—Lath and cement plaster shall conform to IBC, CBC, ASTM guidelines, and veneer manufactures requirements. Allow to cure 72 hours prior to application. We recommend HessLite MAC Scratch & Brown (or PM) to provide a high strength, water-resistant plaster substrate
• Poured in Place Concrete (prepared) and Tilt Up Concrete prepared)—Ensure all form release agents and bond breakers are completely removed; mortar will not bond to surfaces with any trace of release or breaker agents still on the substrate. This is best achieved by removal of the surface layer by bead blasting, grinding or equivalent. The substrate must still be checked to assure complete removal of any bond inhibiting substances. Smooth concrete must be roughened. High pressure washing is typically not adequate for complete removal of bond breakers or release agents. If a bond-ready surface cannot be achieved, install lath and a scratch coat. Concrete should be well cured. 28 days recommended.
• Cement backer board (prepared)—Additional damp proofing / waterproofing may be required in some applications. Application shall be approved by the stone or brick manufacturer. All joints must be taped with fiberglass tape and joints filled with VBM PolyThin Premium, R-Lastic, or equal. Consult cement backer board manufacturer for specific installation recommendations and limitations. A suitable substrate for bonding does not mean it is recommended for all veneer or job conditions.
• Gypsum Board—May be used as a substrate on dry, interior walls only. All joints must be taped with fiberglass tape and filled with VBM PolyThin, R-Lastic™, or equal.
• Ceramic Tile—Existing tile must be sound, well bonded, clean and free of any deleterious substance that may prevent adhesion. Smooth surfaces require roughening to promote bonding. Replace the mix water with R-FlexAd™ latex additive.
• Plywood—Interior applications only. Use only over exterior grade plywood (EGP) 5/8" minimum. Wooden flooring should not have a deflection exceeding 1/360 of span in either dead or live loads. Securing should be done with screw-type nails and glue. A 3/16" gap for expansion should be left around the plywood sheets and surrounding materials. These gaps should be left empty after the installation. Replace the mix water with R-FlexAd™ latex additive.
Mixing Instructions
Proper mixing is critical for designed performance and workability. Please apply the following “best practices” for consistent success using HessLite Bonding Mortars.
• Do not over-mix. Do not mix at high speed. Lengthy and/or high-speed mixing will entrap air in the mix, resulting in lower strengths and poor workability.
• Best non-sag is achieved with mud mixed to a drier consistency. Correct water volume is critical to achieving good non-sag properties—HessLite bondng mortars are mixed at a much dryer consistency than Type-S mortars.
• Allow the mud to slake. The lightweight aggregate in HessLite bonding mortars will continue to absorb water as the mud rests. Then gently remix for 30 seconds. If necessary, adjust consistency by adding additional water. Take note of total water content used and repeat with subsequent batches.
• Test the Bond. Apply mortar to back of veneer and firmly press into the substrate. Wait for one minute, then remove. If mud is mixed properly, there will be equal amounts of mortar on substrate and veneer.
MIXING STEPS
1 • Add VBM PolyThin bonding mortar to clean water (use approximately 4½ to 5 quarts of clean water per 35 lbs. of dry bonding mortar; about 29 to 31% by weight) and mix approximately 3 to 5 minutes at LOW SPEED. Mortars may be mixed in a mechanical paddle mixer or in smaller bucket-batches with a drill and mixing blade. DO NOT OVER MIX to avoid excessive air entrainment.
2 • Allow to slake for 7 to 10 minutes for full hydration.
3 • Gently re-mix and adjust consistency with additional water if necessary.
RESOURCE: HessLite VBM Mixing Guide • (PDF)
RESOURCE: HessLite VBM SPANISH Mixing Instructions Card • (PDF)
Application
Complete the following steps:
1 • First, apply mortar to the substrate with the flat side of a notched trowel, firmly pressing / keying the mortar into the substrate. Next, apply additional mortar to the substrate using the notched side of the trowel. Spread only as much mortar as can be covered in 10 to 15 minutes (to avoid skin-over). Use the correct size notched trowel to make sure veneers are fully embedded (100% coverage). Mortar bed shall be a minimum of 1/4" thick; maximum of 1/2" thick.
2 • Back-butter large veneers and pavers for 100% coverage. Press tile or veneer piece into the wet mortar and beat into place. Do not apply to skinned-over (surface-crusted) mortar. IMPORTANT: Bonding mortar must be firmly pressed onto the surface of the substrate AND veneer piece to assure good contact and bond. Do not simply slide mortar onto the surface. Veneer must have 100% coverage with mortar squeezing out on all sides. For additional installation methods refer to MVMA, ASTMC1780, TCNA, and local building codes. Again, ensure full mortar coverage on both veneer and substrate.
3 • Quality Check: Verify full coverage and bond by periodically removing and inspecting the back of a freshly-applied tile or veneer unit. Note that tile or veneer pieces that have been set for more than 10–15 minutes cannot be readjusted.
NOTE: IT IS THE RESPONSIBILITY OF THE USER TO ENSURE THE MORTAR IS SUITABLE FOR THE INTENDED APPLICATION, THE SUBSTRATE IS PROPERLY PREPARED, AND APPLICATION IS PERFORMED CORRECTLY. PERFORM TEST AND QUALITY CONTROL EXERCISES ON A PRE-CONSTRUCTION MOCK-UP.
Admixtures. *Replacing all or part of the mix water with R-FlexAd™ will increase flexural bond and impact resistance. Recommended for difficult substrates or for areas subject to heavy traffic.
Joint Grouting/Pointing. Use of HessLite MAC Fine Pointing Mortar is recommended. Allow bonding mortars to fully set (minimum 24 hrs) prior to grouting to assure bond is not disturbed. This mortar also contains efflorescence-reducing additives.
Warranty
The technical information and usage statements are based on our best knowledge. The contents of these specifications are presented for informational purposes only and do not constitute responsibility for their use. The manufacturer will replace only that material which is proven defective due to quality of the components or the manufacturing process.
Cautions
Prolonged exposure to dust may cause delayed lung disease. Eliminate exposure to dust. Use NIOSH approved mask for silica dust. Freshly mixed materials may cause skin irritation. Avoid direct contact where possible and wash exposed skin areas promptly. If any cementitious materials get into the eyes, rinse immediately and repeatedly with water and get prompt medical attention.
Note: Testing for crystalline silica (airborne particles of respirable size) has shown no measurable rates of Crystalline Silica (Si02) to be present in HessLite VBM Bonding Mortars.
Warning: Products containing crystalline silica (airborne particles of respirable size) are known to the State of California to cause cancer. For more information go to www.p65Warnings.ca.gov
DATA SHEET: HessLite Safety Data Sheet (SDS) • (PDF)
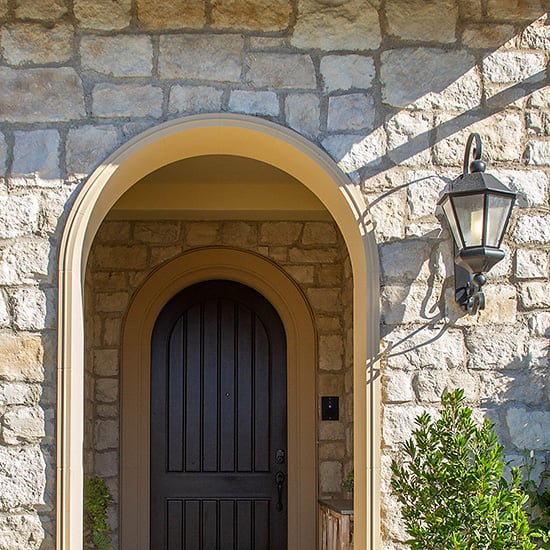
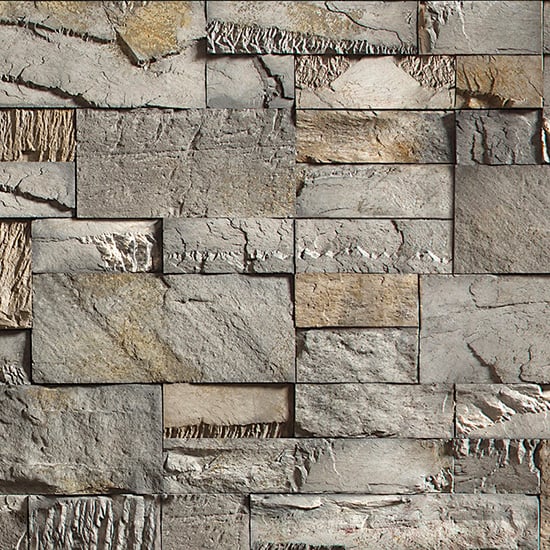
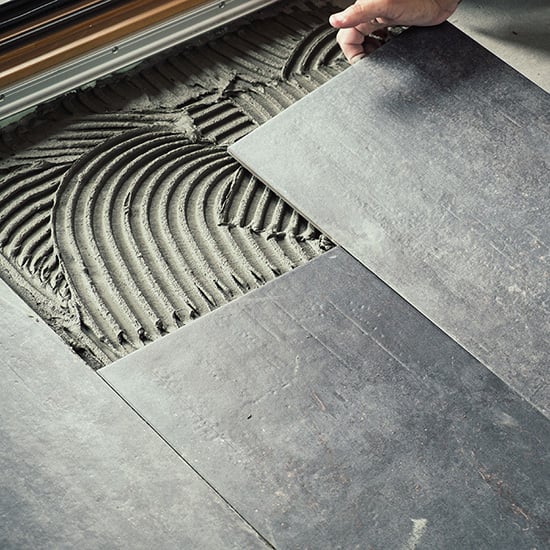
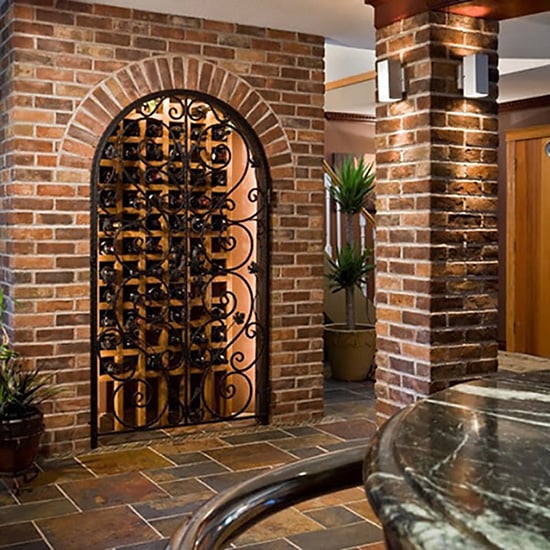
CONTACT US
PRODUCT MANAGEMENT & SUPPORT
Jason (x142) or Matt (x138)
208.766.4777
• • •